Case StudiesCase Studies
- Home
- Case Studies
- Scaling Quality Assurance with Offshore Expertise: Sensyn Robotics leverages SHIFT ASIA for Efficient App Testing
Scaling Quality Assurance with Offshore Expertise: Sensyn Robotics leverages SHIFT ASIA for Efficient App Testing
Company Name | Sensyn Robotics Co., Ltd. |
---|---|
Core Business | Provide business solutions using industrial drones, cameras and smart devices |
Company size | 100 Plus |
Requirements |
|
Sensyn Robotics focuses on technological innovation using cutting-edge robotics to revolutionize different industries and solve social issues. The company uses industrial drones, cameras, and smart devices to automate various tasks such as equipment inspections, disaster response, and surveillance.
However, even with their remarkable strides in technological advancement, Sensyn Robotics faced a significant challenge in ensuring the quality of their software products. As the company embarked on a journey to develop applications integrating drone robotics and AI, they encountered a critical shortage of Quality Assurance (QA) engineers. With Japan grappling with aging infrastructure and a declining workforce due to demographic shifts, the need for rigorous quality control became more pronounced than ever before.
To overcome this QA challenge, Sensyn Robotics embraced offshore testing solutions provided by SHIFT ASIA. This case study delves into how offshore testing played a vital role in driving innovation and excellence in robotics and AI applications at Sensyn Robotics.
The team’s mission & challenges
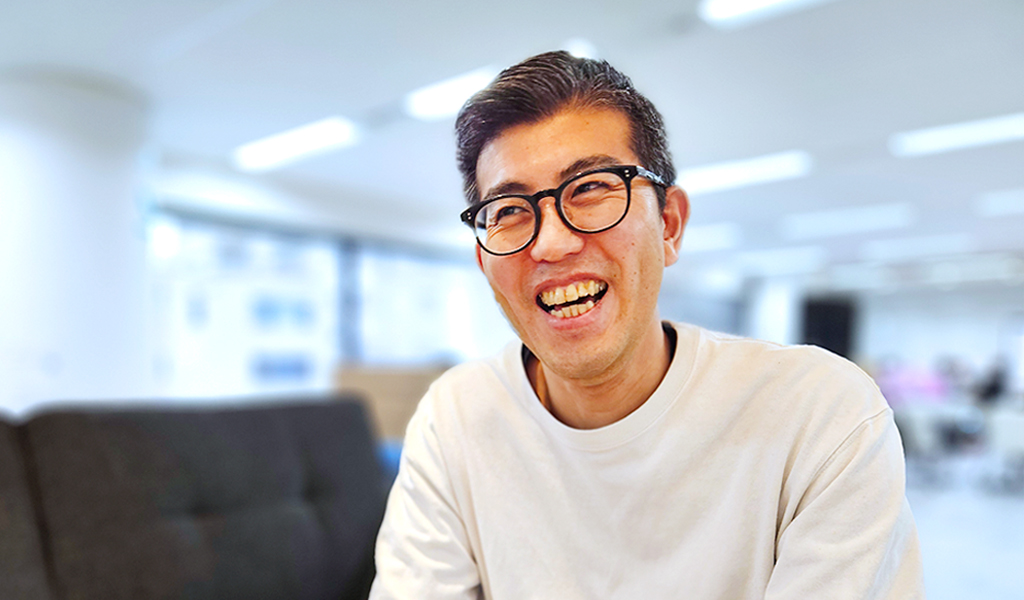
What kind of systems, applications, and services are you developing?
Mr. Takahashi: Japan is facing two challenges: an aging infrastructure and a shortage of workers due to the declining birthrate and aging population. At our company, we are developing an application that combines drone robotics and AI to enable a small number of people to handle maintenance work for aging infrastructure.
Specifically, combining a wide variety of modules based on the cloud platform “SENSYN CORE” with devices such as drones and 360-degree cameras can improve customer operations such as inspecting solar panels and power transmission equipment. It is now possible to build specialized inspection applications with high quality in a short period. About 10 to 20 basic applications can be customized according to customer needs.
What kind of work is the Service Quality Team in charge of?
Mr. Takahashi: Our team responsible for service quality consists of two QA engineers and an SRE engineer who manages the service infrastructure. Our primary responsibility is ensuring the quality of software products, such as systems, applications, and services we create in-house and provide to our customers. We also establish internal security measures and company-wide service operation rules.
Our team is responsible for quality control of about 5 to 6 applications, each taking approximately 3 months. It is important that our quality control is thorough, as even the slightest defect could lead to direct damages such as injury to workers or property damage, particularly in the worst-case scenario when controlling a drone on-site.
What kind of issues did the Service Quality Team face?
Mr. Takahashi: We have a team of only two QA engineers who are responsible for creating test items, conducting tests, and checking for errors. When the Service Quality Team was established, they were only able to work on some development projects. As a result, there was a shortage of manpower for the applications being developed, particularly QA engineers.
This shortage was recognized six months after the establishment of the Service Quality Team. However, owing to cost considerations, there were no plans to hire additional QA engineers. Therefore, the team decided to explore offshore testing as an option to increase the number of QA engineers. Offshore testing has abundant resources and is expected to be highly cost-effective. However, as we have no prior experience in utilizing offshore testing or development, we referred to the opinion of Tsukamoto, who has experience in offshore expertise in China and Vietnam while working at my previous workplace.
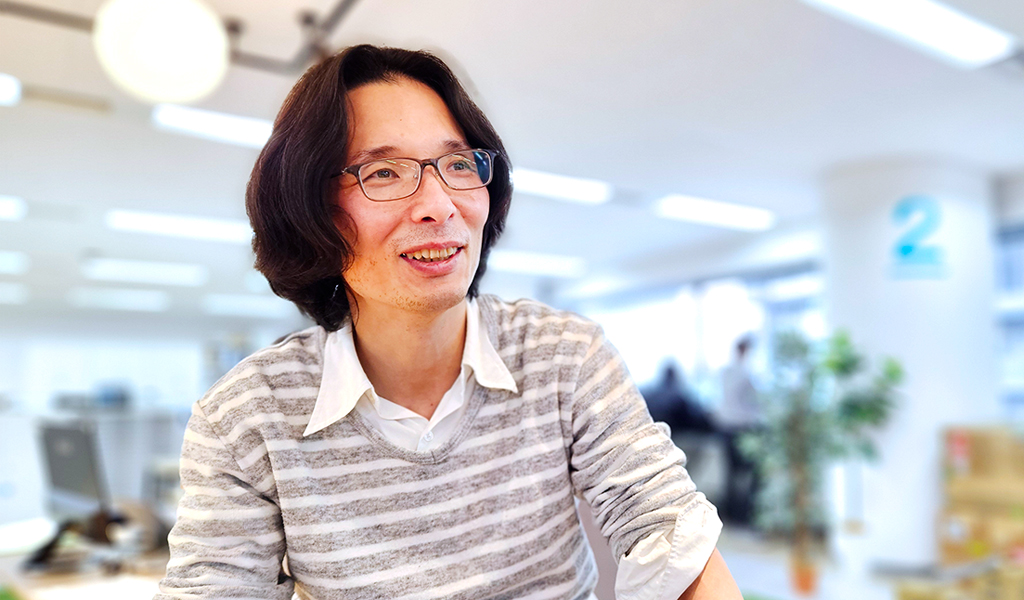
Leverage the power of Offshore testing services
What do you think about the benefits of using offshore testing?
Mr.Tsukamoto: Offshore testing is more cost effective than hiring a Japanese QA engineer. QA engineers in countries like Vietnam are highly motivated and eager to learn. Another advantage is that there are many Vietnamese resources who can speak Japanese, making communication easier. In contrast, Japanese QA engineers may face difficulty in maintaining their motivation levels due to their proficiency in the language. Additionally, I have experience in offshore development in China and Vietnam, and recently, I have noticed that offshore development in Vietnam is becoming more popular. One of the reasons for this shift is the rise in labor costs in China.
What services did you compare and consider to solve the problem of a lack of QA engineers? What factors did you focus on when doing so?
Mr. Takahashi: For this project, we compared SHIFT ASIA’s services with those of two Japanese companies that operate software quality verification businesses.
As Tsukamoto had experienced, offshore testing was highly appealing because it could reduce costs. Additionally, SHIFT Group, including SHIFT ASIA, is known as the largest QA company in Japan, which made them confident in consulting with them. When they inquired about offshore testing using the form, they received prompt responses from QA engineers who provided useful suggestions.
We were worried about the Japanese language proficiency of our QA engineers. However, the person in charge at SHIFT ASIA made every effort to introduce someone with high Japanese proficiency from a Japanese perspective. Our first offshore test was a little nerve-wracking, but thanks to the staff at SHIFT ASIA, we were able to proceed with peace of mind. Finally, they successfully completed the project.
The Japanese language ability and quality of the QA engineers exceeded my expectations. Execute 50-100 test items per week
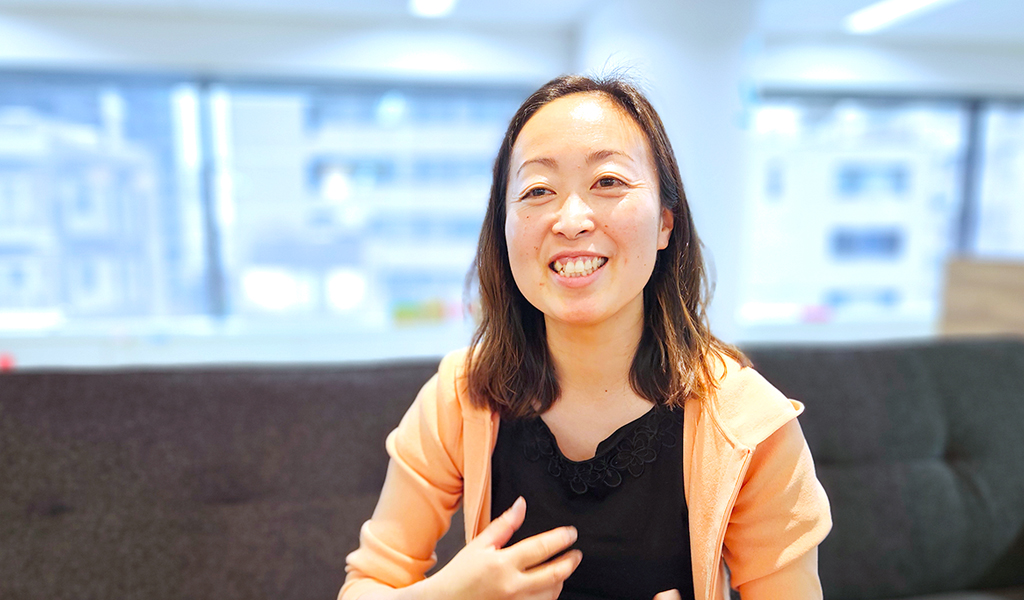
How did the offshore testing efforts progress?
Ms. Kawaguchi: In November 2022, we launched an initiative, and the following month, SHIFT ASIA appointed two QA Engineers to take charge of the project. Both of them had excellent Japanese proficiency and were meticulous in every aspect, from following test procedures to reporting bugs. They left a good impression on me with their level of dedication and professionalism. In case of any ambiguity, they would clearly state, “I don’t understand,” which was helpful in avoiding any misinterpretations of the test items.
Typically, we conduct 50 to 100 test items per week, depending on the level of the test.
What kind of support particularly left an impression on you?
Mr. Takahashi: Our applications are designed to be used with a variety of devices, such as drones and 360-degree cameras. Therefore, it’s important for us to have access to the appropriate devices for testing purposes. In the past, we faced a situation where we needed a 360-degree camera for testing, and they kindly sent the device all the way from Japan to Vietnam. This was very helpful for us. Additionally, we have provided tablet devices with different operating systems for use at construction sites.
Have you ever increased the number of QA engineers?
Mr. Takahashi: When we became overwhelmed with multiple projects or received requests from other teams, we used to bring in temporary staff. Fortunately, we were able to get a response within a week of consulting with the relevant team, which was very helpful. One of the teams requested a 3D master instead of testing the application, but they were able to accommodate this request without any problems.
Moreover, when our assigned QA engineer went on maternity leave, we were able to immediately assign a replacement. It seems that the new QA engineer had properly inherited the work content from the previous person, and there was no disruption to work even after the change.
High quality results
What kind of results have you obtained from your offshore testing efforts?
Mr. Takahashi: In the beginning, the company had only two QA engineers, which limited the number of projects they could handle. However, after working on the SHIFT ASIA project, I feel confident in handling twice as many projects as before. In terms of man-months, we were able to have 30 to 36 man-months. Moreover, we were able to reduce costs to a greater extent than expected. Specifically, we were able to achieve this at about half the cost of hiring one QA engineer as an employee.
How do you evaluate the quality of offshore testing?
Ms. Kawaguchi: When conducting application testing, we have established a comprehensive list of test items for critical components, and they execute them efficiently without taking shortcuts. Furthermore, I would appreciate it if SHIFT ASIA could recommend test items that align with their predefined format. They also provide assistance with test automation, and I was impressed by the high level of quality of the SHIFT ASIA.
This was the company’s first offshore initiative; what kind of reaction did you get from within the company?
Ms. Kawaguchi: At the start of our outsourcing initiative, our company had concerns about the quality of work we would receive from Vietnam. However, when the project began, the Vietnamese QA engineer assigned to us impressed us with their high level of Japanese language proficiency, demonstrated through their communication in our internal business chat. This led to a positive evaluation and changed our initial impression.
In addition to their language skills, the testing quality was exceptional, leading to a shift in our employees’ attitudes towards offshore testing. With reduced psychological barriers, we have now entrusted SHIFT ASIA with offshore development as well.
Utilize offshore testing and automation testing
Please tell us about the outlook for your company’s business.
Mr. Takahashi: Our focus in the future will be on developing applications that utilize AI technology. In order to improve this technology, it is crucial to obtain learning data through repeated tests. As a result, we will continue to manage application quality with a small, elite service team while also making use of offshore testing and automation tools in a flexible manner.
How do you think our offshore testing will be useful in the future?
Mr. Takahashi: We successfully implemented an offshore services initiative that demonstrated our ability to use such services without compromising quality or Japanese language proficiency. Going forward, we plan to leverage offshore services not only for quality assurance but also for application development. We would be delighted if SHIFT ASIA could continue to support us in this endeavor.
Looking Forward
Sensyn Robotics is excited to leverage the power of offshore testing and automation to further enhance their development process. The data gathered through extensive testing will be crucial for refining AI-powered solutions, ultimately contributing to safer and more efficient infrastructure inspections. They envision a continued partnership with SHIFT ASIA as they expand their use of offshore services to drive innovation in the future.
Company Name: Sensyn Robotics Co., Ltd.
Core businesses: Provide business solutions using industrial drones, cameras and smart devices
Website: https://www.sensyn-robotics.com/
ContactContact
Stay in touch with Us